In every organization, part of employees' time is spent on idle, unproductive activities that do not add value to the business. These activities cannot be eliminated completely. However, knowing their type and determining in which parts of the process they occur is a necessary step to idle activities reduction.
In order to be able to optimize processes, it is necessary to understand exactly how much time employees spend on particular activities, and to do this, it is necessary to measure them.
However, in order to gain full knowledge, it is necessary to measure all the activities that the employee performs as part of their duties.
This type of activity is a large area for optimization, and often the people supervising the work of the team do not know exactly what employees are doing outside the system or how much time they spend on activities not recorded on the scanner.
How do we measure non-systemic activities?
Time Harmony gives you the ability to record out-of-system activities on dedicated devices. Scanner data is sent to the system via an interface, and out-of-system activities are measured on Time Harmony devices.
Non-systemic activities consist of process (productive) activities, i.e. those that, although not measured by the WMS, are a necessary part of the process. We will include, for example, cleaning work, folding or wrapping cartons, work in the storage field. On the other hand, unproductive non-systemic activities include, for example, a break or preparation for work after returning from a break or after registering for work.
When we start implementing the system in our clients' companies, we assign specific categories to activities: systemic, non-systemic, standardized, non-standardized, process or non-systemic-unproductive. The exact nomenclature depends on the specifics or the nomenclature adopted in the Client's company.
Measurable data on all employee activities collected in the form of reports will make up a complete picture of working time. The previously mentioned length of breaks, time spent preparing for work, time to take the next action are areas that are worth taking a closer look at and the optimization of which brings quick measurable results.
In addition, the collected data can be compared between locations to correct processes based on good practices derived from data available in the system.
What are the savings of reducing idle activities?
Assuming that the salary of a warehouse worker oscillates at the level of about PLN 4820 gross/month (based on research from December 2023 conducted by Wynagrodzenia.pl), a company employing 1000 warehouse employees will save over PLN 3.5 million over 3-4 months by reducing the level of unproductive activities by 20%.
Idle activities reduction - summary
The presented example shows how much savings can be brought by optimization, which is based on reliable system data on the activities performed. In the course of our long-term cooperation with customers – operators of large logistics and warehouse centres, we receive this kind of feedback very often.
The savings declared by customers consist of a number of aspects resulting from working with the system: improvement of work organization, standardization of processes, increased self-control in terms of punctuality and use of breaks, increase in efficiency and reduction of idle activities possible thanks to the measurement of non-system activities.
Time Harmony is a comprehensive approach to organizing and measuring the work you do.
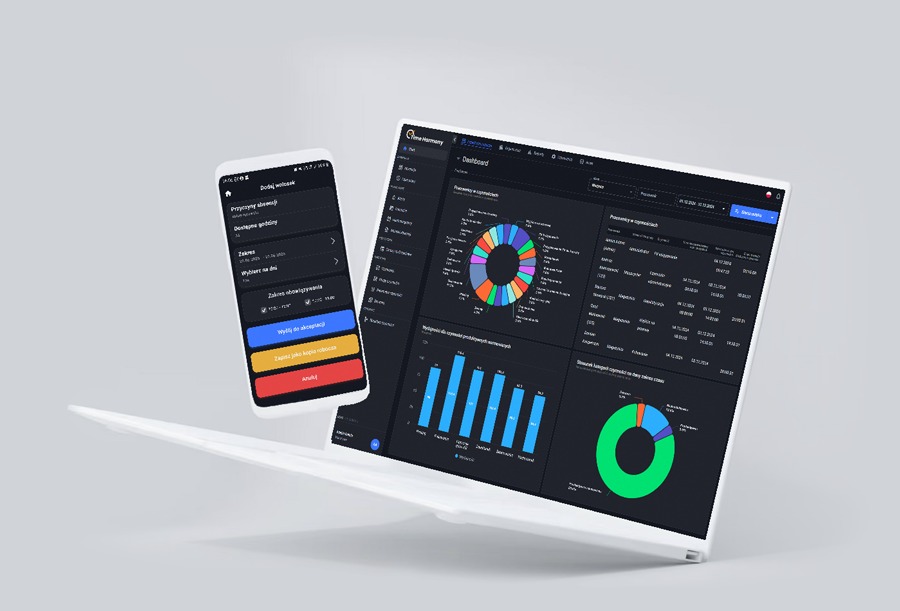
Optimize working time and efficiency of your team